Create Future
The Nurture Room: Interview with Pauline van Dongen
LET'S TAKE CARE OF FASHION TOGETHER.
During the previous edition of MUNICH FABRIC START, you presented the Smart Textile Pop-up Lab at the KEYHOUSE. What was it all about?
The aim of this Pop-up Lab was to familiarize people with smart textiles, and in particular those created by printed electronics. Through my work at Holst Centre (a leading Dutch R&D centre), I see the potential of printed electronics for the textile industry. These printed electronics are thin and stretchable and the printing process allows for a modular design approach. Moreover, they are made using familiar processes, namely through screen-printing conductive inks on flexible substrates like TPU and then heat bonding these smart “trims” onto textile. Visitors of the Pop-up Lab could see this process up close to better understand it and be inspired by the possibilities.




This time, visitors of the fair can book a (free) session in “The Nurture Room”. View the timetable and register here.
What will they experience there?
After having successfully shown the process of printing electronics and their integration in textiles, it is time for the next step. The Nurture Room is a space to reflect and to meet likeminded people who share a wish to do things differently within the fashion industry. It invites open dialogues addressing the urgency to create new relationships between humans and the clothing they wear.
The aim of the sessions at The Nurture Room is to not only inspire participants, but to ensure that they can follow up their inspiration with concrete actions once back in the office. You will be guided through the session by wearable technology experts: Pauline van Dongen and Marina Toeters. By booking a session on a particular topic, such as workwear, outdoor clothing or casual wear, you can tap into a wealth of knowledge and simultaneously help shape the direction of developments in the field of wearables.
The sessions are meant to connect companies covering the full value chain, in order to collectively contribute to new product developments. Together, we will discuss ways to embed technologies into clothing in ways that can nurture people and improve their wellbeing. Visitors will be able to encounter the latest developments that fall within this scope, such as MYSA 2.0: a “relax shirt” that guides the wearer through breathing exercises that can be felt through subtle vibrations along the spine.



Can you tell us a bit more about your own research and how the idea of The Nurture Room relates to it?
In my own research, I focus on the way clothing mediates between our bodies and the world. Our clothes shape how we relate to the world, they actively shape our perceptions and our actions. I look at how we can strengthen our relationship and emotional bond with clothing and, by wearing clothing, with others and with the environment. When our clothes become active and responsive, how will this affect the human-garment relationship for example? My research shows that when we create wearables, we need to take into account the full set of experiential qualities of the garment, and not just the functionality of the technology. I extensively describe this approach in my recent book “A Designer’s Material-Aesthetics Reflections on Fashion and Technology”. It also includes practical guidance for designers and engineers who wish to develop wearables.
As a designer working between the fields of fashion design, textile innovation and technology, I understand these different worlds and know how to connect them. I would like people entering this space to think very consciously about what they want to develop and for whom, what new values the product will bring to people and how they incorporate considerations relating to the well-being of the planet. This ambition is reflected in the concept of The Nurture Room.
Why did you call it “The Nurture Room”?
Nurture is care that is given to someone while they are growing and developing. The term reflects the care with which we should all treat industry. In the context of “nature vs nurture”, the word “nurture” describes the influence of learning and other influences from one’s environment. I experienced how many new things I had to learn when I made a turn to wearables. In wanting to change the system as well as my own position and attitude as a designer, I also noticed that I needed to shed some of the premises that formed the basis for my fashion education. This learning and unlearning are processes that not many people in the industry take the time for or get the time for. While new perspectives are so desperately needed right now. So, to help facilitate this, our main message is: “Come and nurture yourself, by expanding your knowledge in the area of wearable technology.”
Visit The Nurture Room at MUNICH FABRIC START on February 4-6 2020 in Munich, Keyhouse, Booth #34
Due to the limited number of places available for the free individual workshops, we kindly ask you to register by mail to Chantal Gräff at cgr@munichfabricstart.com.
WORKSHOP TIMETABLE
Tuesday, 4th February
11.00 – 11.45 am: sports & activewear
14.00 – 14.45 pm: wool & tailoring
Wednesday, 5th February
11.00 – 11.45 am: workwear
14.00 – 14.45 pm: intimates
16.00 – 16.45 pm: outdoor
Thursday, 6th February
12.00 – 12.45 pm: casualwear
Digital Fabric Lab – The Future Begins Now

Digitization 4.0 is one of the most important topics of the future when it comes to process control within the textile and fashion industry. At the same time, the digitization of fabrics in the preliminary stage of the clothing industry still poses a major challenge.
One of the key building blocks within these technical undertakings will be the digitization of materials and additionals. Digital material parameters such as elasticity, flexibility, tension and rigidity must be determined for the realistic presentation of textiles in product simulation. For these physical measurements, surfaces, colours and textures must be captured and combined in a technologically feasible way.
What this process of analysis looks like in practice, as well as how fundamentally this new achievement changes and accelerates production processes, is demonstrated by a DIGITAL FABRIC LAB which will be featured for the first time in KEYHOUSE.
‘We are convinced that in the future there will be a digital twin for every fabric or button presented. Through an innovative analysis process, the speed of the production process can be increased many times over. ‘
Sebastian Klinder, Managing Director MUNICH FABRIC START
In a community showcase initiated by MUNICH FABRIC START, leading specialist companies and university professionals have joined forces to demonstrate the individual steps in this new type of process in a comprehensive and practice-oriented manner using simulated digitisation stations.





/ STAGE 1 /
# PHYSICAL FABRIC MEASUREMENT
The accurate and informative value of the virtual simulation will on the one hand depend on exact physical parameters for the true representation of the textile material. As well as the transformation into corresponding parameters assigned by the simulation material model and on the other hand it will also depend on exact model calculations.
To describe the material behaviour, the basis weight, the material thickness, the rigidity, the elasticity and the draping behaviour of the textile surfaces can be determined and processed accordingly. This makes it possible for the user to make design and fitting decisions on a purely virtual basis, both for products that will be close to the body as well as those positioned further away.

Technische Universität Dresden
Helmholtzstr. 10
01069 Dresden
Germany
/ STAGE 2 /
# DIGITAL COLOUR COMMUNICATION
Caddon’s multi-spectral technology provides the visually stimulative effects of the design’s colours as well as its spectral data measurements, pixel by pixel in a rapidly captured and communicated image data set, thus making a significant difference to single spectral colour measurement.
With Caddon’s colour digitization, accurate colour values are available where they are needed :
- – in the form of digital colour books with comprehensive colour codes for designers.
- – in the form of digital multi-spectral images for visualisations for production and marketing.


Caddon Printing & Imaging GmbH
Stadionstraße 6
70771 Leinfelden-Echterdingen
Germany
/ STAGE 3 /
# FABRIC SCAN PROCESS
The visual properties of a material sample, sized max. A4, are recorded with the xTex scanner within 1 to 2 minutes. The digitised material is then made into a Tileable, block pattern repeated seamlessly with the help of the xTex software, in a further 5 mintues. Tileable means that it is seamlessly repeated and can be applied to larger areas than initially captured using 3D application.
If necessary, in the following step we can use Caddon’s export colour data to colour or retouch the material using our xTex software for a more accurate colour representation. The finished digital material can then be used in Vidya, for example.

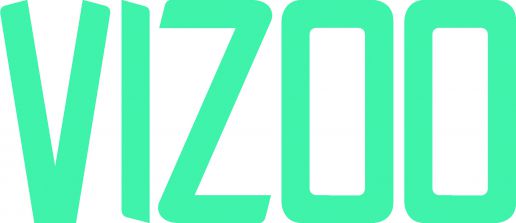
Vizoo GmbH
Johann-Karg-Strasse 30
85540 Haar
Germany
/ STAGE 4 /
# DIGITAL FABRIC SIMULATION & VISUALISATION
3D-Vidya offers the best simulation of cut and material. With 3D-Vidya a piece of clothing becomes digitally visible on the computer, creating realistic decision making bases for designers, product developers and all others involved in the creation process of a collection :
Cutting concepts are visualized.
- – A design becomes immediately visible and can be optimized.
- – Details immediately available including drapery, imprints, ornaments which can be optimally placed.
- – Texture and material properties including elasticity or material thickness, distance to body, gloss structures or wrinkle effects can be precisely represented
- – Fabrics up to 3cm with up to 21 layers can be simulated.
- – Colour management enables the binding of colours to be specified by importing spectral colours and rejecting them under a series of neutral lighting scenarios.


Assyst GmbH
Europaallee 10
67657 Kaiserslautern
Germany
/ STAGE 5 /
# REAL TIME QUALITY ASSURANCE
Based on the speed, transparency and accuracy of Triple Tree Solutions, premium quality management and assurance
solutions is ensured in every stage of textile and apparel manufacturing and sourcing. Using the intuitive and modern user interface, our online quality management system QUONDA visualise all measurements and evaluations throughout the chain. The results are available in real-time and accessible by all members involved, across all devices.
Here at KEYHOUSE we demonstrate the process of colour evaluation, as well as provide a summary and evaluation of the results of the four simulation stations. Digital colour matching between the manufacturer and customer significantly accelerates the procurement process, saves costs and also lowers the carbon footprint of the participating companies by avoiding unnecessary transport – Green Sourcing!


Triple Tree
Kaiserswerther Straße 115
40880 Düsseldorf-Ratingen
Germany
KEYHOUSE - From Poetry to Digitalisation

As a think tank for fashion tech, smart textiles, sustainability and innovation, KEYHOUSE offers concrete approaches for a future-oriented textile and fashion industry. It spans the spectrum from technology to sustainability, from digitalisation to new material resources and manufacturing processes. The mindset of ‘democratic’ research projects, inspiring collaborations and networks as well as high-tech product and process development reflects the pulsating mood of KEYHOUSE at MUNICH FABRIC START.
Those attending include:
Smart Textiles Pop-Up Lab by Holst Centre x Pauline van Dongen featuring interactive workshops on printing electronics on textiles. As a Dutch research hub, the Holst Centre specialises in the development of printed electronics. Unlike conventional electronics, these circuits are thin, lightweight, flexible and even stretchable. They make it possible to make all kinds of products and materials interactive. The material properties of these printed electronics make them particularly suitable for integration in textiles.



KNITCLOUD by N.I.O. combines sustainability and digitalisation with the launch of a personalised 3D knitwear-on-demand brand at the Keyhouse, which as a smart network offers a future-oriented, sustainable answer to today’s overconsumption of clothing. What began with initial tests by start-up company The Girl and The Machine has now developed into a market-ready brand for custom-made 3D knitwear on demand that will be scalable in the future. Knitcloud by N.I.O. (New Industrial Order) will allow brands, designers and web shops to connect virtual designs, body measurement apps, virtual fitting solutions and a digital tailor system (DTS) with a subsequent on-demand ordering system (ONOS). In future, this smart concept will make it possible to produce customised and personalised clothing – as the world’s first open ecosystem for 3D knitwear on demand.
KPMG, one of the leading auditing and consulting firms in Germany, will deliver a unique fusion of business, technology and fashion to the KEYHOUSE this season together with the global IT group Microsoft. This partnership is dedicated to business and technology systems for the fashion industry. The launch of disruptive technologies such as HoloLens, a new POS system, better process management tools and integrated social media engagement will satisfy the modern, demanding customer of the future, ensuring a new era for fashion retailing.

DIGITAL FABRIC LAB
As a joint showcase initiated by MUNICH FABRIC START, the leading specialist firms Assyst, Caddon, Vizoo, Triple Tree Solutions and the University of Dresden have joined forces to present a new type of digitalisation process for fabrics in a comprehensible and practical way through simulated digitalisation stations. The DIGITAL FABRIC LAB demonstrates a new form of analysis process that overhauls production and accelerates it many times over. Digital material parameters such as elasticity, flexibility, tension and rigidity are determined for the realistic use of textiles in product simulation. For these physical measurements, surfaces, colours and textures must be recorded and collated in a technologically presentable way.
‘Digitalisation 4.0 is certainly one of the key issues when it comes to future process controls. One of the essential building blocks within these major technical changes will be the digitalisation of fabrics and additionals. For each fabric and each button there will be a digital ‘twin’.’
Sebastian Klinder, Managing Director MUNICH FABRIC START
SUSTAINABLE INNOVATIONS
Creating alternative materials from unusual resources, instructions for a new approach to textiles and clothing and the rediscovery of traditional crafts – the SUSTAINABLE INNOVATIONS Forum will showcase it all, discover:
-
-
- PHERES & AUXTEX by Eric Esser, with the creation of CAD files thanks to the 3D printing process FDM (Fused Deposition Modelling).
- Atlas of Sustainable Colour(s) by JULIA KALETA as a sustainable colour compass.
- LOOP.A.LIFE with a circular approach to extending the life cycle of textiles.
- LOOP COLLABORATION STUDIO as an integrative movement of socially oriented resource exploitation.
- WORN TO WEAR by Lena Winterink interprets the conscious handling of clothing through the use of copper wire in the yarn.
- SWART LAEKEN by Lotte Gulpers present high-quality items made of premium wool as a sustainable raw material.
- DYELUX by Nikolett Madai uses by-products from the food industry to produce dyestuffs for textiles.
- KNOT by Sanne Visser looks at horn as a raw material from a new angle and creates yarns, ropes and nets from hair.
-




With these selected showcases at KEYHOUSE we give impulses and solutions for a future-oriented use of materials and marketable production processes. This offers great potential for synergies and collaborations, which – used at the right interface and linked together – will have a lasting impact on industry. This season we have once again succeeded in mapping out a broad range of relevant topics for the future.’
Claudia Mynott, Communications Director MUNICH FABRIC START

HIGHTEX AWARD
The HighTex Award will be presented for the 7th time. The MUNICH FABRIC START Innovation Prize honours outstanding initiatives and commitment in the fields of intelligent process solutions, innovative highlights, biotechnology, digitalisation and sustainable innovations.
‘We present the HighTex Award in recognition of outstanding achievements and, at the same time, as a motivation for innovative research projects and thus as a sustainable contribution to a clean future and conscious use of resources.’
Frank Junker, Creative Director, MUNICH FABRIC START

Candidates are assessed according to the following categories: High-Tex, Technology, Smart Fibres, Sustainability, Resource Efficiency, Finishing, Functionality, Health and Circularity Process. An essential principle here is process realisation and marketability. The award winning products and other innovations in the KEYHOUSE HighTex Award Forum will be on display for the entire duration of the trade fair. Supplemented by detailed information on the respective exhibited products including contact information.
SIDE EVENTS
Furthermore, KEYHOUSE offers a comprehensive and exclusive programme of side events throughout the duration of the trade fair. In addition to trend seminars, these include top-class workshops, talks and round table discussions.
The entire lecture programme can be found at >> events.munichfabricstart.com
