Sustainable Materials
Enschede Textielstad by Annemieke Koster
Enschede Textielstad by Annemieke Koster
Until the 1970s, Enschede in the Netherlands, was one of Europe’s textile strongholds, along with Manchester. Then textile production gradually disappeared from the cityscape because it was much cheaper to produce clothes and textiles in low-wage countries. With this however, traceability, protection of workers and sustainability often fall by the wayside – which is why Enschede Textielstad was born out of Annemieke Koster’s desire to bring back transparency along the textile value chain and revive the city’s former traditions.
“I want to bring textiles back to Enschede and make it a city of textiles again – where professionals who still know the craftsmanship of yesteryear pull their knowledge and find innovative approaches. But then in a new, innovative collaboration.”



Local, natural, high quality: In the industrial weaving mill Enschede Textielstad, natural and as locally produced as possible yarns and fabrics for fashion and home textiles are created. The basis for this is formed by fair and environmentally friendly raw materials that are sourced exclusively from well-known suppliers: guaranteed Made in Europe – for shorter transportation routes and a smaller environmental footprint. Enschede Textielstad’s offers various options: Readymade fabrics produce bestsellers for direct purchase, Made To Order fabrics are woven but can be customised, or Custom Made fabrics for particularly individual ideas, new fabrics or for recycling product waste – so there is something to suit everyone.
Chiengora instead of Angora
Yarnsustain by Ann Cathrin Schönrock & Franziska Uhl
Often, solutions for ethical and sustainable are not used, even when they are the most obvious one. Fashion and knitwear designer Ann Cathrin Schönrock and textile engineer Franziska Uhl have searched the market in vain for sustainable and at the same time high-quality yarns which led the duo to get creative themselves: They founded the company Yarnsustain to revolutionise the fashion and textile industry with yarns and fabrics made from dog hair.
“The wool industry currently imports high-quality fibers from around the world, while the source is often walking directly in front of our faces. With us making this resource available to the textile industry, we are able to correct this systemic error. Pet-based high quality wool enables everyone out there to contribute to a better textile future.“



Back in 2017, Ann Cathrin Schönrock, who is a dog owner herself, started working with her dog’s wool – because why shouldn’t this material, which is actually considered waste, also be used for clothing or to fill home textiles? Together with her co-founder Franziska Uhl, she developed the high-quality Chiengora®, a yarn made from the undercoat of long-haired dogs. Support by funds from the German government, the organisation was able to collect more than two tonnes of undercoat this year alone and process it into yarn.
Behind the company are the NGO Saving Lost Resources e.V., Yarnsustain and the brand company modus intarsia. In this triad, the founders contribute to animal welfare, produce high-quality yarns and sell garments made from dog hair – to further promote consumer acceptance and establish garments made from dog hair on the market.
From Trash to Treasure by Youyang Song
Dutchman Simon Angel has found a talented designer whose innovation makes it possible to create textiles from recycled bioplastics. The curator of SUSTAINABLE INNOVATIONS presented these and three other developments during the FABRIC DAYS.
„More and more, we are moving towards an era of adhocracy. Transferring this into the material and textile world: Materiality and comfort will experience a comeback”, explains Simon Angle in our interview with him.
An example of this is presented here as part of the SUSTAINABLE INNOVATIONS:
FROM TRASH TO TREASURE BY YOUYANG SONG
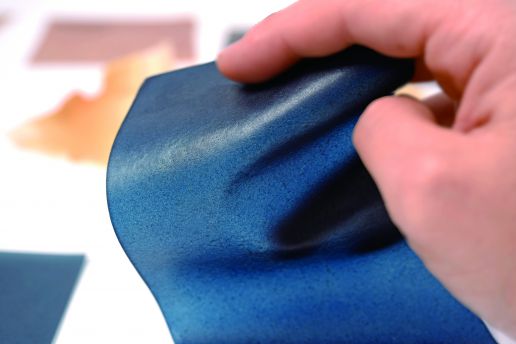
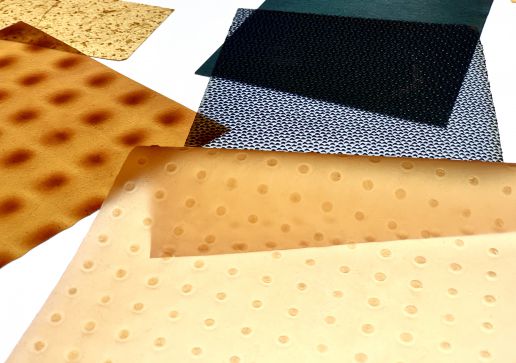

How can innovative products be created without using new resources? How can we stop growing mountains of waste? Use the old to create the new: The designer and materials researcher Youyang Song has set herself the goal of helping to develop an ecosystem consisting of purely biodegradable materials. Handbags made of banana peel, lampshades made of soy milk – the designer processes organic waste into new recyclable materials. This results in products that can be returned to the natural cycle at the end of the product life cycle.

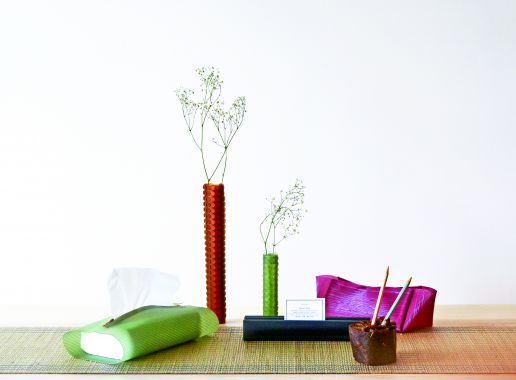
„Our goal is to establish a circular economy regarding the materials and follow the sustainable development guidelines to create our products.“
Youyang Song
Song has developed the “Cooking new materials” technique, in which fruit peels or soy milk are mixed with a natural binding agent. “APeel” is the name of the soft, innovative material created by this process. The natural product is also waterproof and robust like real leather, smells fruity, has a natural texture and is completely biodegradable. Protecting the environment in style: With her project, Song wants to show that environmentally friendly products can be not only practical, but also aesthetic and stylish.

Perfect Imperfection by Studio Mend
FABRIC DAYS presented futuristic innovations of international manufacturers. Besides, Sustainable Innovations curator Simon Angel introduced innovative developments of young designers in the SUSTAINABLE INNOVATIONS forum.
“Rethinking old traditions and adding a contemporary note to them can create innovation – sometimes you don’t have to come up with something entirely new to be innovative”, states Simon Angle in our interview with him.
An example of this “traditional innovation” is:
PERFECT IMPERFECTION BY STUDIO MEND
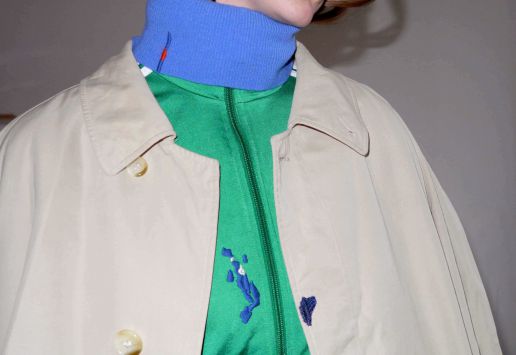
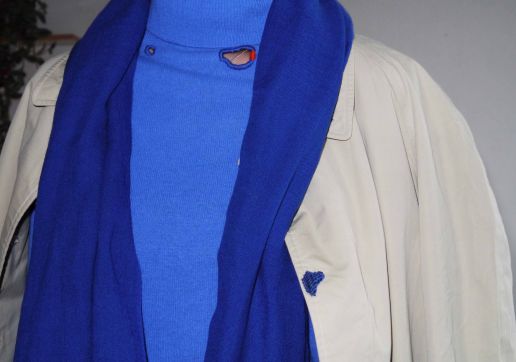
A new pair of jeans for 29,99€, a t-shirt for 7,99€. Constantly changing trends, synthetic fabrics and inferior quality: Since fast fashion conquered the world in the 1960’s, new clothes are available everywhere and at all times. What is broken is thrown away and what is no longer in fashion lies unused in the cupboard. More than two million tonnes of textile waste are generated annually in the European Union alone. When did our relationship to clothing change in such a way? This question was asked by the young fashion designer Sunniva Amber Flesland. She founded Studio Mend in 2019 to bring back the emotional and material value of what we wear.
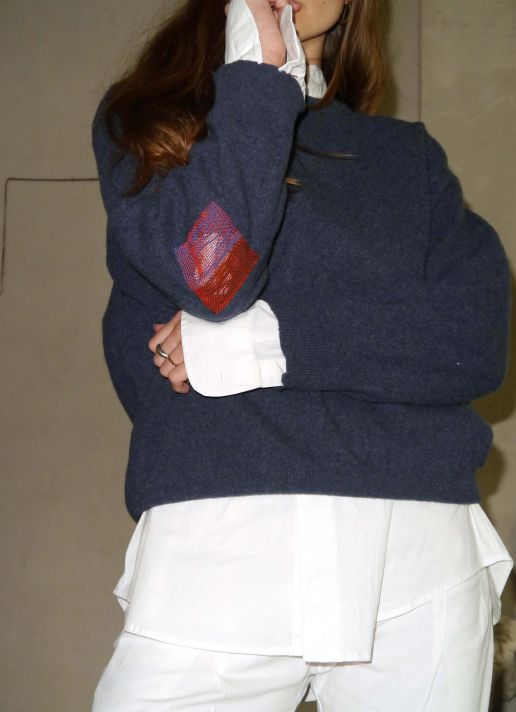
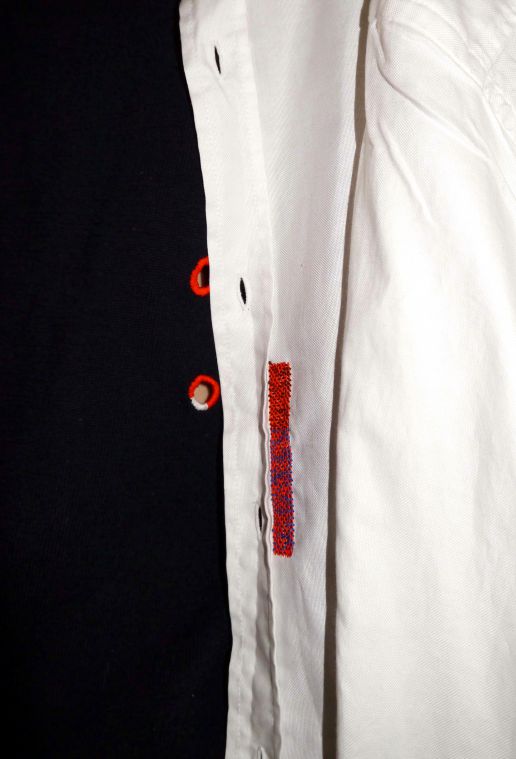
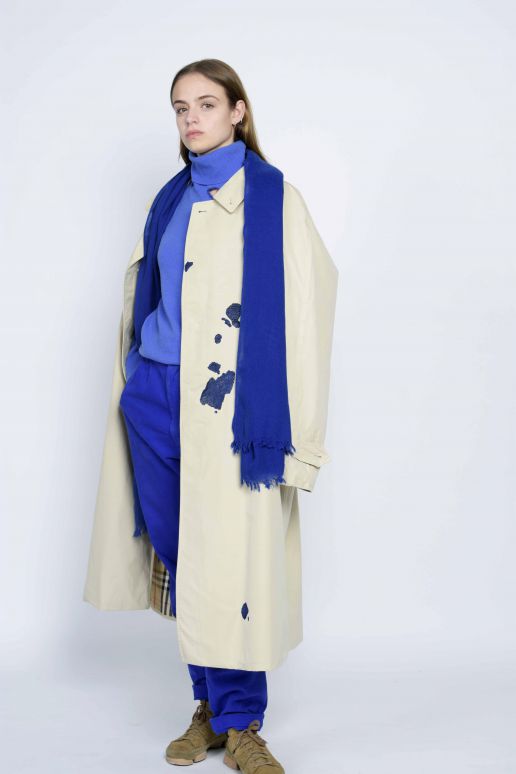
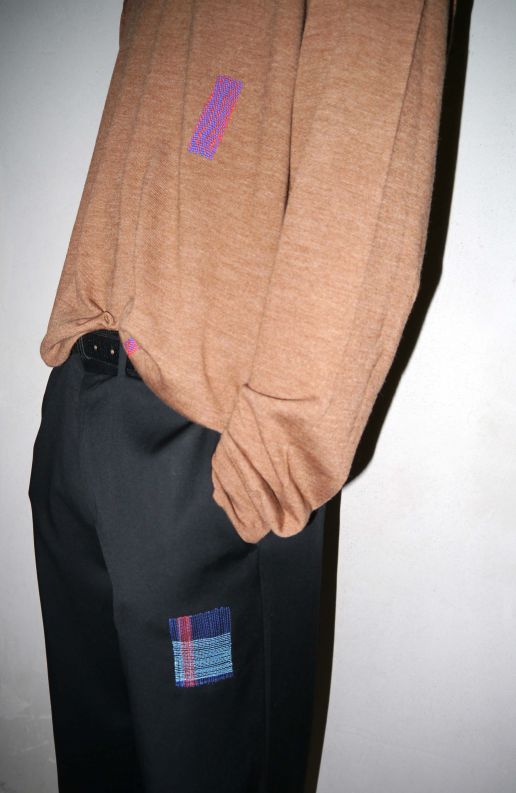
“I am excited by raw material, old crafts and traditions, beauty, and looking for potential where it’s not easily seen.”
Sunniva Amber Flesland
Appreciate, repair, refine: At Studio Mend, traces of wear and tear from through the lifespan of the garments are repaired in a very special way. Island Weave, Edge Mend, Pinstripe Patch, Crossover Stitch: The customer can choose between these four carefully developed technical styles to make his or her damaged favourite piece whole again. In combination with individual colour designs, valued and unique pieces are created. The acceptance of transience and imperfection – this is the basic principle of the Japanese philosophy Wabi Sabi, which served as inspiration for Flesland. Instead of hiding faults, they are celebrated as signs of an eventful life. Visibly and ingeniously, the artist creates valuable, aesthetic and unique pieces as a statement for a better fashion world.

Living Material by Iris Bekkers
SUSTAINABLE INNOVATION Autumn.Winter 21/22 #1
SUSTAINABLE INNOVATIONS curator Simon Angel presented four developments for the season Autumn.Winter 21/22 at FABRIC DAYS at the beginning of September. The Dutchman is always on the search for interesting young designers, outstanding innovations and the latest novelties in the textile world.
In our latest interview with him, he stated: “With the Sustainable Innovation forum, we present the near future and showcase what already is possible.”
Let us now present you the first of this season’s SUSTAINABLE DEVELOPMENTS:
LIVING MATERIAL BY IRIS BEKKERS

Doesn’t fit anymore, doesn’t fit properly: Many of our favourite pieces of clothing lose their shape after a short time and are shipped directly to the nearest garbage dump. Textiles that adapt to individual body shapes and external conditions could reform the fashion and textile industry.
To create such textiles, product designer Iris Bekkers uses auxetic materials in her project “Moving Structures”, i.e. stretchable materials that can adapt their structure to their surroundings. As part of her final project at Eindhoven University of Technology, she has developed a special face mask that not only adapts to different face shapes, but also adapts its filter function to the environment and is very breathable.




More comfort, longer wearing time, less waste: Due to their geometric structures, auxetic materials become thicker when stretched, rather than thinner like most fabrics. The potential of such fabrics ranges from jackets that adapt to the seasons and can therefore be worn in summer and winter, to shoes that change their flexibility and stability as required. Bringing the material to life: For her designs, Iris Bekkers not only thinks about the material and its texture, but also about the context in which the fabrics are used and enjoyed. Only in this way can her designs combine man and nature.
“The auxetic samples are the start and inspiration for a range of products that can adapt and transform themselves, functioning optimally in different circumstances. The potential for adaptability results in more value, more function and a reduction in the quantity of materials and products necessary.”
Iris Bekkers



SUSTAINABLE INNOVATIONS, Big Changes & New Challenges
An interview with SUSTAINABLE INNOVATIONS curator Simon Angel – the Dutchman who is always on the search for interesting young designers, outstanding innovations and the latest novelties in the textile world. You will find Simon and the four SUSTAINABLE INNOVATIONS he chose this season in the foyer of hall 4 at FABRIC DAYS.
- Simon, what new innovations can we expect this season?
Rethinking old traditions and adding a contemporary note to them can create innovation – sometimes you don’t have to come up with something entirely new to be innovative. This edition ‘the new thing’ is referring to something old like weaving, repairing and recycling. For example, weaving with solar-panels from Pauline van Dongen, repairing as value-creation from Studio Mend or value adding applications by Auxetics and industry ready, recycled bioplastic fabrics by Studio YouYang. All these projects use traditional crafts and materials, but in a new and innovative way.
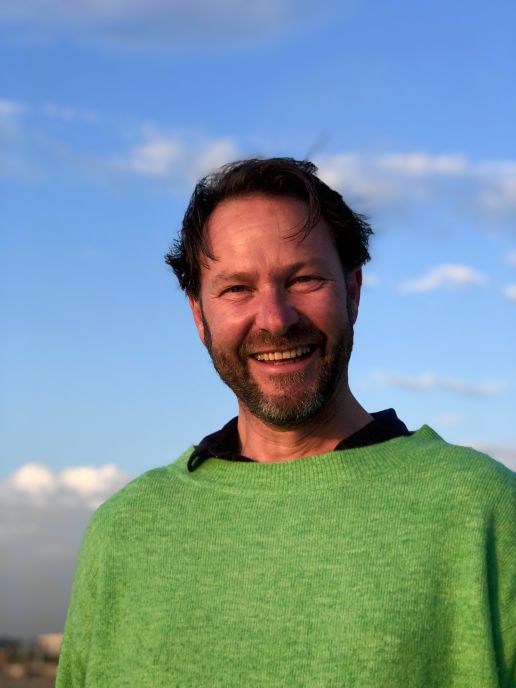
2. In 2020, the Corona pandemic brought the world to an unscheduled stop. But the crisis has also sped up the movement towards a more sustainable lifestyle. How will this shape innovation?
As you know, I’m an optimist. This year’s developments actually encouraged change. How you look at things makes a big difference in order to get yourself in the right inspired mode. Pandemics or heatwaves are nature’s way of confronting us. Just like we are experiencing changes in our environment, the nature experienced changed by humans for years and is now responding to us. All this is leading us to a dialogue with nature – a much needed one. Bit by bit we realise we exist as part of nature. Designers, scientists, the industry and consumers change their habits and question old methods. Finally, most of us start to realise what is necessary to ultimately save our world. We can only achieve that, when we are searching to find the balance with ourselves and with nature.

- It is the sixth time that you are curating the SUSTAINABLE INNOVATIONS. How has this year’s edition been different?
The responses to sustainable innovations are new. The dialogue is getting serious. For example, have a look at the location of the Sustainable Innovations forum this year: It has moved from the Keyhouse to the main hall, right in the heart of the industry. Right at the spot where the big changes happen.
- This year’s innovations are all about the material: textiles created out of biowaste fabrics, adapting its shape to the environment – can you give us a glimpse into the material of the future?
With the Sustainable Innovation forum, we present the near future and showcase what already is possible. As you can see, this future finds its inspiration in old traditions, crafts and resources. But what comes after that? It is hard to predict as the world is losing its linearity as we know it. More and more, we are moving towards an era of adhocracy. Transferring this into the material and textile world: design and shapes will not be the main focus of designers anymore. Materiality and comfort will experience a comeback – and we will have to redefine the product development process and all that entails. We have to open our minds and let go of expectations. We have to source from our universal knowledge to create something that in this form has never been there before.
- How can we see the current situation as an opportunity to innovate, rather than for all the challenges it presents?
This situation shows on a holistic level, that humans have to develop themselves and challenge the Status quo. Enjoy the experience as it opens up new horizons which we could never have dreamt of. Look at the Munich Fabric Start, with the Fabric Days they showed how to deal with unforeseen obstacles and ever changing circumstances – a pretty good demonstration of a future recipe for attitude, mental shift and permanent dialogue. So yes, let’s see every day as a chance for a better tomorrow.
Learn more about Simon’s sustainable novelties for the season Autumn.Winter 21/22 during the three days of FABRIC DAYS from 1 – 3 September 2020 at MOC Munich.
FABRIC DAYS AUTUMN.WINTER 21/22
OPENING HOURS
1 SEPTEMBER 2020 · 9.30 AM – 6.30 PM
2 SEPTEMBER 2020 · 9.30 AM – 6.30 PM
3 SEPTEMBER 2020 · 9.30 AM – 4.00 PM
LOCATION
MOC Munich | Halls 1 – 4 Ground Floor
Lilienthalallee 40
D – 80939 Munich
Sustainable Standards Guaranteed at ReSOURCE
With increasing importance placed on sustainability, the need to guarantee truly sustainable standards is in greater demand by buyers and brands. Ahead of their showcase at ReSOURCE at the next edition of MUNICH FABRIC START, we interviewed representatives Heike Hess of the International Association of Natural Textiles (IVN) and Franziska Dormann of Global Organic Textile Standard (GOTS).
Briefly, IVN awards two quality seals for ecologically produced products: NATURTEXTIL and NATURLEDER. For both seals, the association has defined parameters that have become a standard in the industry. The association is co-owner of GOTS, the worldwide standard for the production of sustainable textiles on an industrial scale.




What is the most frequently asked question at the beginning of a consultation?
GOTS: Often it begins with a general introduction to the Global Organic Textile Standard, i.e. What is covered by the standard? How is this ensured? By reviewing the strict social and environmental criteria throughout the entire textile supply chain – from the fields to the wardrobe – GOTS guarantees safety and transparency for the consumer. The independent certification ensures credibility compared to mere self-explanatory statements.
IVN: Most visitors ask us for certifications and seals. How to get certified, which fabrics and accessories must be sourced to reach IVN BEST or GOTS requirements or how do our seals differ from others founds in ReSOURCE, register here.
What changes do you want brands to make in the next 5 – 10 years to bring about and anchor sustainable aspects of the textile industry?
GOTS: I think most people have recognized the importance and urgency of this because no one can fly under the radar for long. Sustainability interests those who have to justify themselves the most. For us, these are the brands that sell. Everyone involved is interested, the question is which actions follow? In industry, the spectrum ranges from greenwashing to genuinely practiced sustainability. Consumers range from lip service to showing a real willingness to spend more on sustainable products.
IVN: Many buyers, especially brands, are looking for certified fabrics. The selection of certified fabrics made with natural fibres in ReSOURCE is quite large, but for synthetic and regenerated fibres there is a lack of products that have been awarded truly sustainable seals. I would like to see more interest from the brands here, which would result in a stronger commitment on the part of the fabric suppliers.


How has the brands’ approach to research and purchasing changed over the last seasons?
GOTS: The trade fairs, as well as specific enquiries by e-mail, have resulted in more and more brands wanting to find out which suppliers are already GOTS-certified. Here I refer to the public database with almost 6,000 certified companies. Many companies that are interested in GOTS want to continue working with their existing suppliers and therefore jointly go the way of gaining certification of their entire supply chain.
IVN: You can clearly see that the topic of sustainability is becoming increasingly important for brands. Visitors at ReSOURCE are better prepared and ask more concrete questions. Many are looking for specific products and have clear expectations about what a fabric should be like. The typical length of time brands exhibit in the ReSOURCE area has definitely increased. More and more buyers who do not explicitly belong to sustainable companies are also showing interest in the products exhibited at ReSOURCE.

What are the specific challenges facing a future-oriented fashion industry?
IVN: The challenges vary depending on the size and orientation of the fashion companies. Smaller brands – especially in the sustainable segment – have problems finding certified suppliers who also supply small quantities. Larger companies use many different materials and accordingly many different suppliers. It is difficult to have an overview of the entire supply chain up to your own company, especially if you attach importance to a certain level of sustainability held by suppliers and sub-suppliers. It is still a challenge to reconcile certification and sustainability with the profitability of products. For particularly fashionable brands, it is still challenging to find exclusive or unique fabrics and additionals in sustainable qualities. There are certainly some other challenges, but overall it is more important that today means making sustainable fashion easier and more profitable than it was a few seasons ago.


