Material Innovation
Seaweed Design by Violaine Buet
Seaweed Design® by Violaine Buet
In the beginning, there was her desire to work with a natural, living material. Violaine Buet’s choice intuitively fell on seaweed, the ancient marine plant that formed part of the landscape of her childhood in Brittany. The overarching goal of her efforts: To develop an innovative expertise on seaweed to use it in art, haute couture, scenography and decoration as well as visual merchandising and industrial manufacturing. Because: seaweed can be used in many ways. Whether weaving, dyeing, sewing, printing, embossing, tufting, engraving, braiding or pressing – the possibilities seem almost unlimited.



With her craftsmanship as a designer, Violaine Buet explores the aesthetic and technical properties of the material, develops natural dyeing methods with the support of experts in vegetable dyeing and biopolymer researchers. Using interdisciplinary methods, she combines expertise with craftsmanship, inspired by weavers, leather workers, jewelers, tailors, screen printers, gilders and master glaziers. In this way, she not only creates customised textiles from the biodegradable algae, but also walls, landscapes and installations.
“It’s like writing a story with an inevitable factor of time. With seaweed I have to take into account seasons, species, tides, weight, smell, particularities, colour-fade, hydrophilicity and decomposition, all of which change with time. It’s about everything coming together in a kind of balance.”
Violaine Buet
Pre-Loved by Sarmite Polakova
Pre-Loved by Sarmite Polakova
Turning old into new: material and product designer Sarmite Polakova along with designer Mara Maizele have created a completely new textile concept with their biotextile Pre-Loved. Pre-Loved consists of used textile waste and natural binders. With this product, the designers want to question the traditional concept of fabrics and shift the perspective to recycled mixed fibres. Shoddy is the name for the material made from unsaleable and no longer wearable garments. Cotton, polyester and wool: Shoddy consists of a variety of fibers that are combined into a single mass in the recycling process.



Another special feature is Shoddy’s excellent insulating properties. The biotextile can be used for a wide variety of purposes: in a warming winter coat, in a cosy couch or in a well-insulated house wall. Through colour separation, controlled patterning and even natural dyeing, the fabric also stands out with a unique look. What’s more, the short fibers, which are otherwise unsuitable for spinning yarns, are combined with bioplastics that strengthen the fibers from the inside out and give the material a smooth, leather-like surface. With Shoddy, a whole new kind of man-made fiber is created – Pre-Loved celebrates this new textile identity, bringing a new aesthetic and highlighting the former life of each worn garment through nuances of colour and texture.
“When textile waste meets bio-plastics and together they form a new leather-like material for future fashion applications.”
Sarmite Polakova
Fixing Fashion by Alicia Minaard
Copying Desired - Fixing Fashion by Alicia Minaard
Sharing knowledge, saving clothes: 3.3 years – that’s the average lifespan of one piece of clothing. With good care and a few tricks, clothes can last much longer. The digital platform Fixing Fashion has made it its goal to help those interested in caring for their favourite pieces, repairing them themselves or recycling them. On Fixing Fashion, users can find ideas, tips and instructions for protecting worn clothing with creative approaches. Designer Alicia Minaard prepared for this together with the organisation One Army for over two years: In interviews, workshops and excursions, Minaard’s network researched the best practices and methods for recycling and repairing discarded clothing worldwide – and is now making them available free of charge. The result is a collection that you can’t buy, but should imitate or use as a source of inspiration for your own Fixing Looks.



But the Fixing Fashion team is not only concerned with providing information. Rather, the initiators of the project would like to build up a community that exchanges ideas and supports each other in preserving clothing for longer – and thus, not least, in saving textile waste. By carefully caring for textiles, their lifespan can be increased from 3.3 to 4.5 years. According to the American textile waste volume, this could save 1.22 million tons of waste per year.
“The collection is not for sale. Instead, each look is merely meant to inspire. In a way it is meant to trick people, as if this is a brand but then really it has everything and you need to do it yourself!”
Alicia Minaard
New Blue Circular Denim
New Blue - A new circular denim material by Tim van der Loo & Sandra Nicoline Nielsen
Buy, wear, throw away – that’s what happens to most clothes. That’s where the principle of a circular economy comes in: Worn clothing can be much more than waste and becomes part of new and continuous material flows.
What began in 2018 as a project for a master’s thesis at the Weißensee Academy of Art in Berlin is currently supported by Re-FREAM, part of the STARTS (Science + Technology + Arts) initiative under the European Commission’s Horizon 2020 research and innovation programme.
“New Blue explores new pathways in circular economy, aesthetics and production. Denim is a ubiquitous material which is loved and used by many. It is also a significant source of waste. The challenge as we see it is to find a way to recirculate old worn out jeans and left over fibers within the system.”



Denim was always considered a particularly durable material – until it lost its integrity due to increasing globalisation and rapid consumption. With New Blue, the new circular denim, material and product designer Tim van der Loo and techno-anthropologist Sandra Nicoline Nielsen want to change that. In their process, jeans as raw material are cut into small fibres and then bonded to form a fleece. Using a new technology using digitally assisted industrial embroidery, the pattern is made directly on the fleece. Through a unique technique, the areas defined by the embroidery remain intact when the fleece is washed, while the non-embroidered parts of the fleece dissolve on contact with water and can eventually be reused as raw material. In this way, New Blue makes circular and waste-free production of denim a reality.
Enschede Textielstad by Annemieke Koster
Enschede Textielstad by Annemieke Koster
Until the 1970s, Enschede in the Netherlands, was one of Europe’s textile strongholds, along with Manchester. Then textile production gradually disappeared from the cityscape because it was much cheaper to produce clothes and textiles in low-wage countries. With this however, traceability, protection of workers and sustainability often fall by the wayside – which is why Enschede Textielstad was born out of Annemieke Koster’s desire to bring back transparency along the textile value chain and revive the city’s former traditions.
“I want to bring textiles back to Enschede and make it a city of textiles again – where professionals who still know the craftsmanship of yesteryear pull their knowledge and find innovative approaches. But then in a new, innovative collaboration.”



Local, natural, high quality: In the industrial weaving mill Enschede Textielstad, natural and as locally produced as possible yarns and fabrics for fashion and home textiles are created. The basis for this is formed by fair and environmentally friendly raw materials that are sourced exclusively from well-known suppliers: guaranteed Made in Europe – for shorter transportation routes and a smaller environmental footprint. Enschede Textielstad’s offers various options: Readymade fabrics produce bestsellers for direct purchase, Made To Order fabrics are woven but can be customised, or Custom Made fabrics for particularly individual ideas, new fabrics or for recycling product waste – so there is something to suit everyone.
Chiengora instead of Angora
Yarnsustain by Ann Cathrin Schönrock & Franziska Uhl
Often, solutions for ethical and sustainable are not used, even when they are the most obvious one. Fashion and knitwear designer Ann Cathrin Schönrock and textile engineer Franziska Uhl have searched the market in vain for sustainable and at the same time high-quality yarns which led the duo to get creative themselves: They founded the company Yarnsustain to revolutionise the fashion and textile industry with yarns and fabrics made from dog hair.
“The wool industry currently imports high-quality fibers from around the world, while the source is often walking directly in front of our faces. With us making this resource available to the textile industry, we are able to correct this systemic error. Pet-based high quality wool enables everyone out there to contribute to a better textile future.“



Back in 2017, Ann Cathrin Schönrock, who is a dog owner herself, started working with her dog’s wool – because why shouldn’t this material, which is actually considered waste, also be used for clothing or to fill home textiles? Together with her co-founder Franziska Uhl, she developed the high-quality Chiengora®, a yarn made from the undercoat of long-haired dogs. Support by funds from the German government, the organisation was able to collect more than two tonnes of undercoat this year alone and process it into yarn.
Behind the company are the NGO Saving Lost Resources e.V., Yarnsustain and the brand company modus intarsia. In this triad, the founders contribute to animal welfare, produce high-quality yarns and sell garments made from dog hair – to further promote consumer acceptance and establish garments made from dog hair on the market.
From Trash to Treasure by Youyang Song
Dutchman Simon Angel has found a talented designer whose innovation makes it possible to create textiles from recycled bioplastics. The curator of SUSTAINABLE INNOVATIONS presented these and three other developments during the FABRIC DAYS.
„More and more, we are moving towards an era of adhocracy. Transferring this into the material and textile world: Materiality and comfort will experience a comeback”, explains Simon Angle in our interview with him.
An example of this is presented here as part of the SUSTAINABLE INNOVATIONS:
FROM TRASH TO TREASURE BY YOUYANG SONG
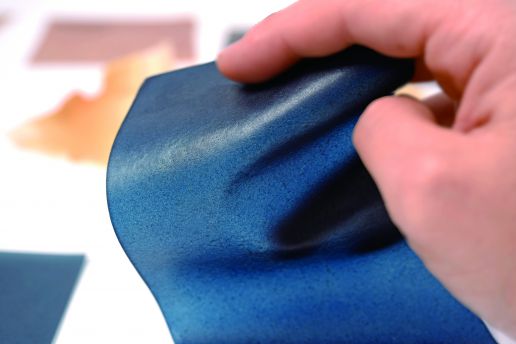
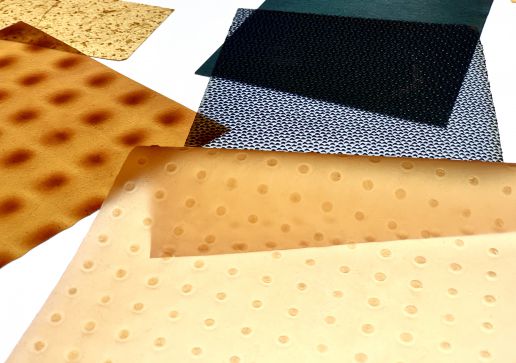

How can innovative products be created without using new resources? How can we stop growing mountains of waste? Use the old to create the new: The designer and materials researcher Youyang Song has set herself the goal of helping to develop an ecosystem consisting of purely biodegradable materials. Handbags made of banana peel, lampshades made of soy milk – the designer processes organic waste into new recyclable materials. This results in products that can be returned to the natural cycle at the end of the product life cycle.

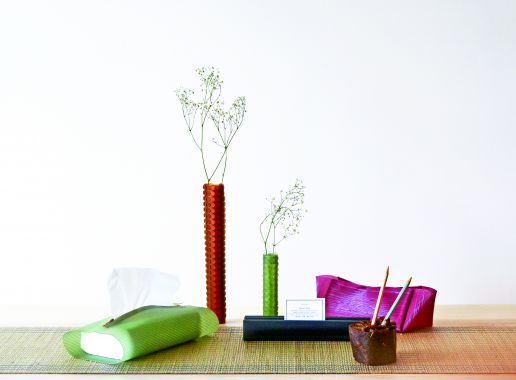
„Our goal is to establish a circular economy regarding the materials and follow the sustainable development guidelines to create our products.“
Youyang Song
Song has developed the “Cooking new materials” technique, in which fruit peels or soy milk are mixed with a natural binding agent. “APeel” is the name of the soft, innovative material created by this process. The natural product is also waterproof and robust like real leather, smells fruity, has a natural texture and is completely biodegradable. Protecting the environment in style: With her project, Song wants to show that environmentally friendly products can be not only practical, but also aesthetic and stylish.

Perfect Imperfection by Studio Mend
FABRIC DAYS presented futuristic innovations of international manufacturers. Besides, Sustainable Innovations curator Simon Angel introduced innovative developments of young designers in the SUSTAINABLE INNOVATIONS forum.
“Rethinking old traditions and adding a contemporary note to them can create innovation – sometimes you don’t have to come up with something entirely new to be innovative”, states Simon Angle in our interview with him.
An example of this “traditional innovation” is:
PERFECT IMPERFECTION BY STUDIO MEND
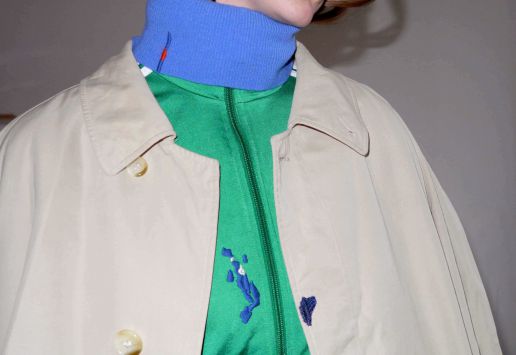
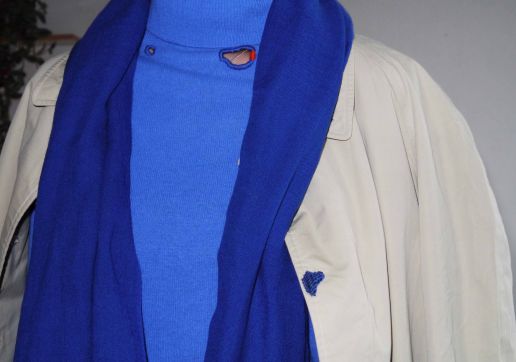
A new pair of jeans for 29,99€, a t-shirt for 7,99€. Constantly changing trends, synthetic fabrics and inferior quality: Since fast fashion conquered the world in the 1960’s, new clothes are available everywhere and at all times. What is broken is thrown away and what is no longer in fashion lies unused in the cupboard. More than two million tonnes of textile waste are generated annually in the European Union alone. When did our relationship to clothing change in such a way? This question was asked by the young fashion designer Sunniva Amber Flesland. She founded Studio Mend in 2019 to bring back the emotional and material value of what we wear.
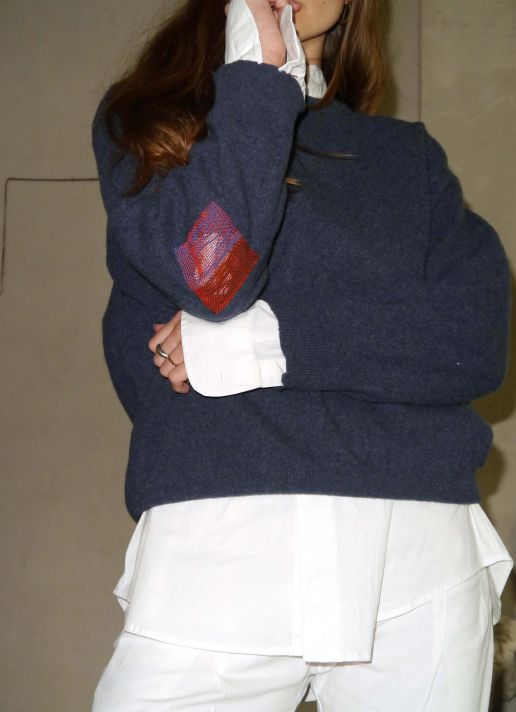
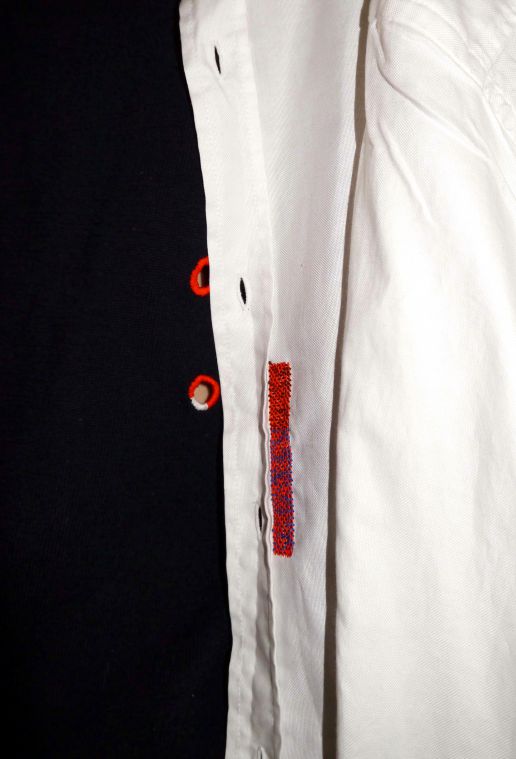
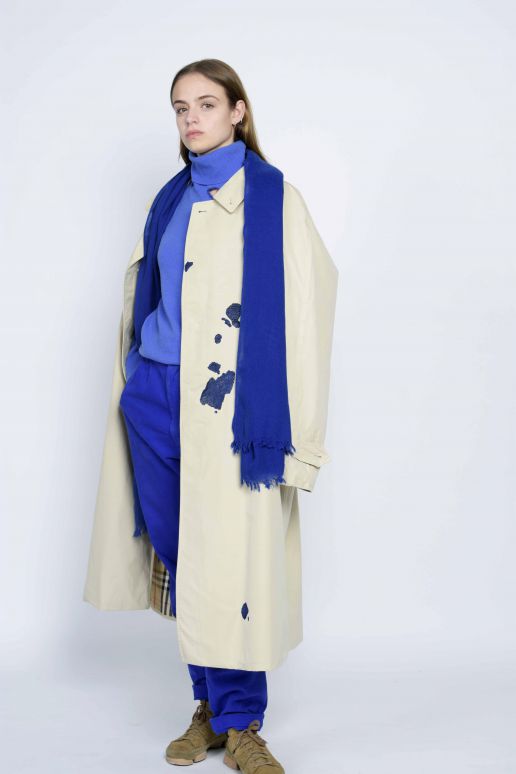
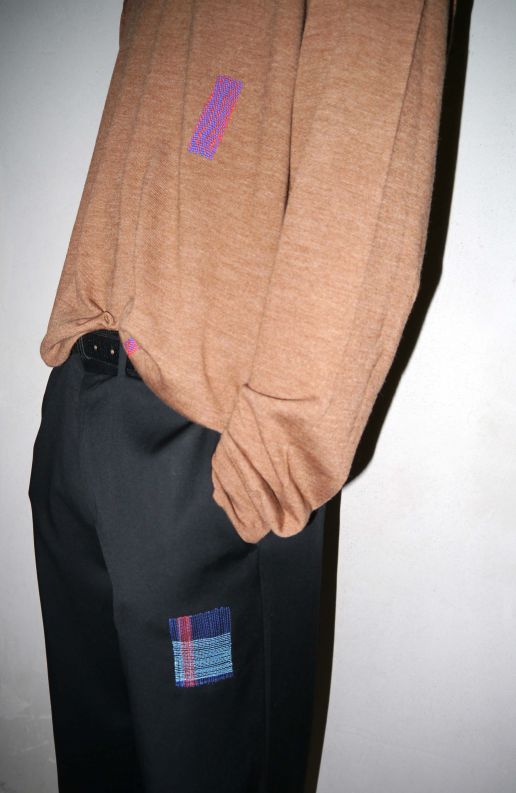
“I am excited by raw material, old crafts and traditions, beauty, and looking for potential where it’s not easily seen.”
Sunniva Amber Flesland
Appreciate, repair, refine: At Studio Mend, traces of wear and tear from through the lifespan of the garments are repaired in a very special way. Island Weave, Edge Mend, Pinstripe Patch, Crossover Stitch: The customer can choose between these four carefully developed technical styles to make his or her damaged favourite piece whole again. In combination with individual colour designs, valued and unique pieces are created. The acceptance of transience and imperfection – this is the basic principle of the Japanese philosophy Wabi Sabi, which served as inspiration for Flesland. Instead of hiding faults, they are celebrated as signs of an eventful life. Visibly and ingeniously, the artist creates valuable, aesthetic and unique pieces as a statement for a better fashion world.

Living Material by Iris Bekkers
SUSTAINABLE INNOVATION Autumn.Winter 21/22 #1
SUSTAINABLE INNOVATIONS curator Simon Angel presented four developments for the season Autumn.Winter 21/22 at FABRIC DAYS at the beginning of September. The Dutchman is always on the search for interesting young designers, outstanding innovations and the latest novelties in the textile world.
In our latest interview with him, he stated: “With the Sustainable Innovation forum, we present the near future and showcase what already is possible.”
Let us now present you the first of this season’s SUSTAINABLE DEVELOPMENTS:
LIVING MATERIAL BY IRIS BEKKERS

Doesn’t fit anymore, doesn’t fit properly: Many of our favourite pieces of clothing lose their shape after a short time and are shipped directly to the nearest garbage dump. Textiles that adapt to individual body shapes and external conditions could reform the fashion and textile industry.
To create such textiles, product designer Iris Bekkers uses auxetic materials in her project “Moving Structures”, i.e. stretchable materials that can adapt their structure to their surroundings. As part of her final project at Eindhoven University of Technology, she has developed a special face mask that not only adapts to different face shapes, but also adapts its filter function to the environment and is very breathable.




More comfort, longer wearing time, less waste: Due to their geometric structures, auxetic materials become thicker when stretched, rather than thinner like most fabrics. The potential of such fabrics ranges from jackets that adapt to the seasons and can therefore be worn in summer and winter, to shoes that change their flexibility and stability as required. Bringing the material to life: For her designs, Iris Bekkers not only thinks about the material and its texture, but also about the context in which the fabrics are used and enjoyed. Only in this way can her designs combine man and nature.
“The auxetic samples are the start and inspiration for a range of products that can adapt and transform themselves, functioning optimally in different circumstances. The potential for adaptability results in more value, more function and a reduction in the quantity of materials and products necessary.”
Iris Bekkers



Tejidos Royo are next to present with ReSOURCE at VIEW
Tejidos Royo are longstanding exhibitors at our BLUEZONE Denim Trade Show as well as VIEW Premium Selection and now they will be among the first to present their sustainable fabrics with ReSOURCE at VIEW.

How important is it to you, to present your new products at VIEW Premium Selection?
VIEW & MUNICH FABRIC START means quality and efficiency. Always thinking about the future, these fairs are constantly changing with the sole objective of satisfying the needs of the exhibitors and visitors. At Tejidos Royo we share this philosophy, and we are also aware of the relevance that both the VIEW fair and Munich Fabric Start have in Germany for the textile sector. We have been betting for this fair for many years, due to the importance that the German market has for Tejidos Royo.
Our goal is that the fabrics presented in each edition, serve as a source of inspiration for visitors. This new AW 20/21 collection has SUSTAINABILITY and the use of the most advanced technology in the development of fabrics as main characteristics, together with an exceptional quality of finish.
Sustainability is not just a trend. Please tell us how intensely you are working on this topic right now?
NSustainability has been imposed as the only recipe to counteract the ecological crisis of the planet. For many critics, sustainability is for the fashion industry a facelift. But the change is not only in a “green washing” rather the change comes from a complete revolution of all the production processes of a company.
The buying trend among consumers is changing. The consumer no longer only looks for price, quality, speed, exclusivity, etc. but among its purchasing decisions is the sustainability and social-environmental commitment of the company. The term ‘Sustainability’ in the private sector is escalating as a strategic priority. It is not just about selling more products to more people. It is about limited resources, climate change, over-population which challenge innovation to make more competitive products.
Tejidos Royo, aware of the seriousness of the situation, continues to guide the textile industry towards this new era of sustainability and the protection of human rights throughout the value chain by innovative solutions.
“Our goal is to give the market the best product without permanent harmful effects for the future.”
The trajectory of Tejidos Royo is marked by the development of leading-edge sustainable techniques in the industrial process.


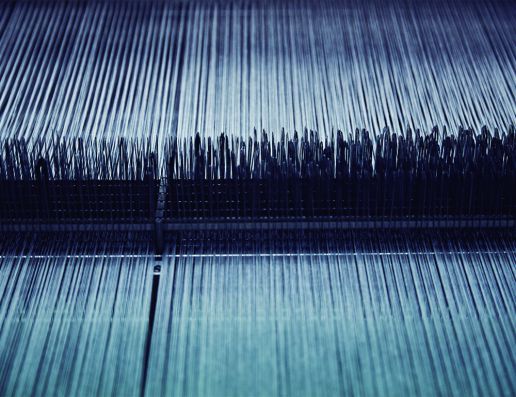

Today Tejidos Royo is a pioneer in the development of a unique process in the world, capable of dyeing indigo without using water. This process, developed together with Gastón Company and IMD- and denominated DRY INDIGO®, gets the requirements to be considered an eco-sustainable technology to Indigo Yarn Dyeing process with Zero Consumption and Zero Discharge of Water, to Process Certified by AITEX.
How does this influence the future of your company?
We are aware of the effort we are making in terms of investment, but also that, if we do not act, we will end the planet. Our continuous search for sustainable solutions throughout the value chain influences us in a positive way and gives us the peace of mind that we are on the right track. The mentality of the textile sector is changing. It is a slow process, but both, manufacturers, brands and consumers are adapting to this new way of creating and consuming fashion that is increasingly sustainable and beneficial in all aspects, by and for the common good. A new way of doing things has arrived and we are firmly committed to it.
Please highlight some of the sustainable products visitors will find in your upcoming collections at VIEW Premium Selection and MUNICH FABRIC START.
DRY INDIGO® The future of sustainable denim, IS NOW
Tejidos Royo, together with Gaston and Imd, has developed the Dry Indigo® technology, a dyeing process which is unique in the world. This certified and guaranteed technology under the ECO – TECHNOLOGY by AITEX (textile research institute) allows to dye indigo yarn with zero water in dyeing process, 89% less chemicals, 65% reduced energy usage and also zero water discharge. In addition to being the most sustainable dyeing technology in the market today, our Dry Indigo® registered brand offers this features in the fabric:
- Intense Cast (Indigo intense hue)
- Multi Cast Wash-down (being a superficial dyeing, it allows very sharp contrasts)
- Very versatile fabric to laser processing
ROYO has the exclusive right of this unique technology worldwide.
REBOOT LINE “Recycled PFD fabrics”
This fabric is the first sportswear recycled fabric in PFD (Prepared For Dye), characterized by premium quality and regular finishes that solves “the big problem” of the presence of foreign fibers in the spinning and dyeing process of recycled sportswear fabrics. Its most outstanding features are:
- Recycled Pre-consumer
- Non foreign fibers and clean look
- Same look and hand-feel of conventional fine cottons
RECYCLED DENIM FABRICS
We support the shift towards an efficient and traceable economy in the use of resources, an upcycling strategy of responsible product based, fundamentally, on the use of pre and post-consumer textile waste “close the loop” to manufacture new fabrics improving their benefits. All through the circular process. All items containing more than 20% recycled material have the international external guarantee “Global Recycled Standard” (GRS), which strengthens the credibility of all the products we obtain.
“We have the opportunity to reduce the consumption of natural resources and guarantee an optimum quality.”


Do you have any questions regarding ReSOURCE? Feel free to contact us at any time.