Sustainability
Fabrics Spring.Summer 24 I
In the FABRICS Area, around 600 international suppliers present their material innovations for all apparel segments. The complete product portfolio of fashionable woven and knitted fabrics made of wool, cotton, silk, blends and functional fibers is represented here. For the Spring.Summer 24 season, we present some highlights from international producers in our FABRICS blogposts:
ATHENEA
Athenea is much more than just a family textile company founded in 1976 in Alicante, Spain. Athenea has managed to keep all the production process internal, which allows them to be recognised as a vertical factory with the ability to develop qualities, print (digital as well as conventional), dye and finish. There’s no limitation in the number of colours nor the scale of the designs. They can 100% personalise the designs following their clients’ specifications, therefore creating unique and exclusive designs.




BOGAZICI ORME
Bogazici Orme is one of the industry’s leading companies which is specialized in producing / exporting jacquard knitted fabrics since 2006.
Developing new items before client request, delivery on time, invest in research and development are the principles lead us to success. They serve their passion, high quality and trust to their clients.
The collection offers recycled polyester / organic cotton and other eco-friendly materials. Furthermore a wide range of fancy yarn development is available and they are able to produce for Inditex and Join life.

GLOBAL TEXTILE
Global Textile is one of the largest textile companies in the Republic of Uzbekistan, specializing in Yarn and Knit fabrics.
The company started operations in 2018 and is now vertically integrated in the production of textiles, from growing cotton to production of garments and apparel. The company grows its own cotton with the latest drip irrigation technology, has its own cotton processing plants, the largest spinning mills in Uzbekistan located in Tashkent and Fergana, including knitting and dyeing houses in Fergana. They have ISO, Usterized, Oeko-tex certificates, that confirm the quality, safety and environmental properties of their products.

THIS MIGHT BE ALSO INTERESTING FOR YOU
Smart Knitting – Sustainable Innovations
3. August 2023
When the programmers of KNITWEAR LAB teamed up with 3D software specialists, a completely new idea for more sustainable, cost-efficient and design-oriented pattern development and knitwear production emerged.
The Fabric Trends Autumn.Winter 24/25 – Part I
1. August 2023
Stripes and checks are often seen in Autumn/Winter 2024-2025, tone on tone or through vibrant, ethnic colours. Checks bring movement to these colours and are in high demand as light and elegant checks.
The clothing of the future – Sustainable Innovations
27. July 2023
Bye bye, plastic! The long-term goal is to be able to replace virgin polyester as a raw material.
MUNICH FABRIC START – closing report
21. July 2023
The most important fabric trends for Autumn.Winter 2024/25, lectures and discussions on the most relevant industry topics as well as plenty of networking opportunities:
THE COMEBAG PROJECT
18. July 2023
A team of young fashion designers has realised a great upcycling project over the last few weeks: they have sewn unique bags from former trade fair materials such as flags, various trade fair banners and carpet left overs from the MFS.
Bluezone Highlights
15. July 2023
The 5 DENIM SENSES are brought to live thanks to the generous support from Naveena Denim Mills who provided the denim fabrics for this project.
Trend Preview for AUTUMN.WINTER 24/25
13. July 2023
Trendbook and Colour Code offer the ideal inspiration and information basis for the development of your Autumn.Winter 24/25 collection...
THE SOURCE 2023 – Autumn.Winter 24/25 – Part II
6. July 2023
Bold geometric jacquards, mini checks and 3D textures are telling a story about clean-cut contrasts in Union 3 Fashion’s Fall-Winter Collection.
Visbatex – Performance by nature
4. July 2023
Das Münchner Unternehmen entwickelt in seinem eigenen Nature Tech Lab High- Performance-Stoffe auf Basis von Bambusviskose (Anteil von mindestens 50 %).
CONNEXXION – SAAT MUNICH
29. June 2023
SAAT bedeutet im Indischen „gemeinsam“ und im Deutschen „was aus gesätem Samen entsteht“. So ist die Mode von SAAT eine harmonische Verknüpfung verschiedener Faktoren, die stets Neues hervorbringt.
KEYHOUSE 2023
Im atmosphärischen Industriecharme des KEYHOUSE, der Halle 5, zeigen progressive Anbieter und Global Player aus branchenübergreifenden Bereichen ihre aktuellen Neuentwicklungen und Innovationen. Auf über 1.000 Quadratmetern finden Sie richtungsweisende Smart Textiles, Future Fabrics und neue Technologien – sei es in Punkto Nachhaltigkeit, Kreislaufwirtschaft, Digitalisierung, Traceability, Technologie oder Finishing. Inszeniert als interaktiver Think Tank stehen zukunftsweisende Show Cases neben Sustainable Innovations im Spotlight.
Im KEYHOUSE befindet sich auch das Hauptvortragsforum der MUNICH FABRIC START mit exklusiven Keynotes, Podiumsdiskussionen, Trend Präsentationen, Q&A Sessions & Experten-Talks internationaler Branchen-Insider. Dies sind einige der innovativen Brands, die ihre Neuheiten während der letzten KEYHOUSE Edition im Januar 2023 präsentiert haben.
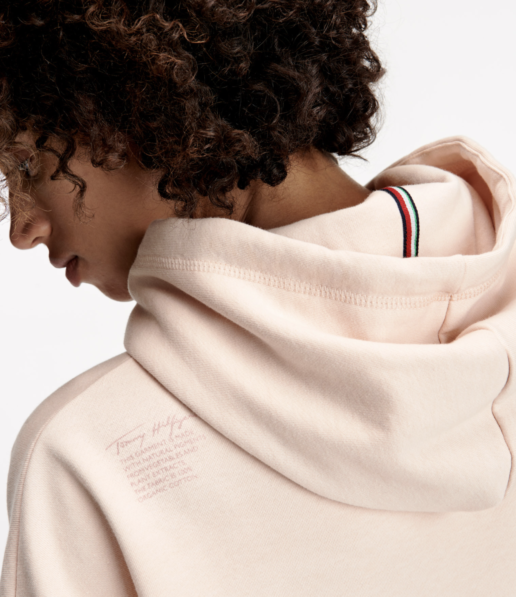
FICUS INNOVATIONS
Stellen Sie sich eine Technologie zum Färben von Textilien vor, die im Vergleich zu herkömmlichen Reaktivfärbemethoden mehr als 50 % Wasser und Energie spart. Stellen Sie sich außerdem vor, dass sie natürliche Pflanzenabfallextrakte als Farbstoffe und Hilfsstoffe für alle Vor- und Nachbehandlungs- und Färbeprozesse verwendet. Ficus Innovations hat seine einzigartige Technologie zum Färben von Naturstoffen nach 7 Jahren R&D entwickelt. Ziel ist es, natürliche Ressourcen zu schützen und wiederherzustellen, indem die Einführung nachhaltiger Stofffärbe-, Druck- und Veredelungsprozesse beschleunigt wird.

KAISER & DYSTAR
Der türkische Laundry-Anbieter Kaiser hat kürzlich das Advanced Used-Look-Konzept für modische Wash-Down-Effekte lanciert. Dieses Verfahren nutzt einzigartige und nachhaltigere Methoden, um mit einer neuen Farbstoffgruppe namens Lava Dye OZN einen Used-Look auf farbigen Kleidungsstücken zu erzielen. Das Advanced Used Look-Konzept biete eine einzigartige Lösung für die Probleme des Marktes in Bezug auf Kosten, Echtheit, Reproduzierbarkeit und Nachhaltigkeit bei used Non-Denim-Looks mit wasserlosen Methoden und der speziellen DyStar-Chemie.


MONTEGA
Rapid Dry ist das revolutionäre Produkt von Montega, das den Trocknungsprozess verkürzt und einen Mehrwert für das fertige Kleidungsstück schafft. Dank seiner speziellen Formel ermöglicht Rapid Dry eine schnellere Verdunstung des Wassers in der Faser, Energieeinsparung während der Trocknungsphase und folglich niedrigere Kosten für den gesamten Prozess, wodurch ein saubereres Kleidungsstück mit weniger Verschleiß erzielt wird.
REACTIVE REALITY
Reactive Reality ist der führende Anbieter von Technologien zur virtuellen Anprobe und zur Erzeugung virtueller Modebilder. Die PICTOFiT-Plattform ermöglicht es Modemarken und Einzelhändlern, virtuelle Umkleidekabinen und fotorealistische Avatare nahtlos in ihre Website, App und In-Store-Lösungen zu integrieren. Für Verbraucher erstellt die Plattform fotorealistische Avatare von Käufern, die genaue Größenempfehlungen für alle Marken ermöglichen. Die Avatare können interaktiv eingekleidet werden und bieten unbegrenzte Outfit-Kombinationen und virtuelle Hintergrundszenen.

TORAY INTERNATIONAL EUROPE
Toray ist ein integrierter Chemiekonzern, der seine Geschäftstätigkeit in 29 Ländern und Regionen weltweit ausübt. Das 1926 gegründete Unternehmen ist ein weltweit führender Hersteller von fortschrittlichen Materialien und ein Lösungsanbieter mit Schwerpunkt auf Fasern, Textilien und Bekleidung.
Das könnte Sie auch interessieren
Smart Knitting – Sustainable Innovations
3. August 2023
When the programmers of KNITWEAR LAB teamed up with 3D software specialists, a completely new idea for more sustainable, cost-efficient and design-oriented pattern development and knitwear production emerged.
The Fabric Trends Autumn.Winter 24/25 – Part I
1. August 2023
Stripes and checks are often seen in Autumn/Winter 2024-2025, tone on tone or through vibrant, ethnic colours. Checks bring movement to these colours and are in high demand as light and elegant checks.
The clothing of the future – Sustainable Innovations
27. July 2023
Bye bye, plastic! The long-term goal is to be able to replace virgin polyester as a raw material.
MUNICH FABRIC START – closing report
21. July 2023
The most important fabric trends for Autumn.Winter 2024/25, lectures and discussions on the most relevant industry topics as well as plenty of networking opportunities:
THE COMEBAG PROJECT
18. July 2023
A team of young fashion designers has realised a great upcycling project over the last few weeks: they have sewn unique bags from former trade fair materials such as flags, various trade fair banners and carpet left overs from the MFS.
Bluezone Highlights
15. July 2023
The 5 DENIM SENSES are brought to live thanks to the generous support from Naveena Denim Mills who provided the denim fabrics for this project.
Trend Preview for AUTUMN.WINTER 24/25
13. July 2023
Trendbook and Colour Code offer the ideal inspiration and information basis for the development of your Autumn.Winter 24/25 collection...
THE SOURCE 2023 – Autumn.Winter 24/25 – Part II
6. July 2023
Bold geometric jacquards, mini checks and 3D textures are telling a story about clean-cut contrasts in Union 3 Fashion’s Fall-Winter Collection.
Visbatex – Performance by nature
4. July 2023
Das Münchner Unternehmen entwickelt in seinem eigenen Nature Tech Lab High- Performance-Stoffe auf Basis von Bambusviskose (Anteil von mindestens 50 %).
CONNEXXION – SAAT MUNICH
29. June 2023
SAAT bedeutet im Indischen „gemeinsam“ und im Deutschen „was aus gesätem Samen entsteht“. So ist die Mode von SAAT eine harmonische Verknüpfung verschiedener Faktoren, die stets Neues hervorbringt.
Designers as game changer - ASSYST
Sustainability:
Designers as game changers
Creativity up and costs under control – that’s the true heart of sustainability.
At the Assyst Experience, creative designers will see how they can have a huge influence on material consumption.
Designers as game changers
At the Assyst Experience, creative designers will see how they can have a huge influence on material consumption.
Purchasing and production are usually responsible for sustainability. However, you can significantly influence costs, material consumption and profitability if you think beyond reusable fabrics – and the key to this is in the hands of apparel designers.
Shaping sustainability and profitability with 3D
Nowadays, development in 3D is everywhere. Optical prototypes help to save samples during approval procedures. How sustainable and cost-efficient the entire development process actually is becomes apparent as soon as the design draft moves on to technical product development. Most 3D design software is not based on production-safe patterns. If important information for product development and production such as seam allowances and sizing & fitting is missing, the pattern must be changed and re-approved in 2D. Physical samples are then necessary, despite the 3D design. Not so with Assyst.
Achieving a better hit rate for designs – without any physical samples
The Assyst 3D design software is always based on a production-oriented 2D pattern that supports a seamless process from 3D through to production. This ensures greater sustainability and cost efficiency. Because a digital product has already been created in the design you can decide on the look, but also whether the sizing & fitting is correct and what the later production result will be. These advantages are evident in the entire process – but especially in design, where time is tight. The more efficient this phase is, the less burdensome it will be for all departments. Development can be cut short to just a few days instead of weeks.
Buying and producing precisely the right amount of fabric
In the digital development process data flows from production to design just as easily and quickly as from design to production. This is important because a lot can be achieved at the beginning of the process. Let’s assume that the 3D design software is networked with order optimization. If so, all the participants can estimate the fabric consumption and material costs from the first draft and quickly introduce countermeasures if the product costs deviate in any way from the collection framework plan. Companies can also negotiate in a more targeted manner and only have as much fabric produced as is needed.
Always the correct production result for color, material and sizing & fitting
All the elements of a clothing product can be digitally controlled in the process. Color can be captured precisely and sent to supply partners. These values serve as exact references for quality control. Digital fabrics with the textures and properties of the actual materials help creative designers with product simulation and facilitate remote decisions.
Thinking of new ways
If the product is entirely digital, it makes sense to become creative in the process and drive innovations like automation. Not only fabric developments but also knitting designs can be developed digitally, visualized in 3D for a sizing & fitting check and then transferred straight to the knitting machine.
The Assyst Experience – a new event format for digital design
At the Assyst Experience, these topics will come alive for you! Exemplary processes give designers ideas for implementation in their own companies, and lectures on key topics of the industry complete the program.
Discover more industry-changing innovations at our upcoming trade shows:
100 % collagen, 0 % plastic - Sustainable innovations
100 % collagen, 0 % plastic
GOLD by WINT Design Lab Robin Hoske and Felix Rasehorn
Sustainable Innovations
If you think that “GOLD” by WINT Design Lab was inspired by the shiny precious metal, you’re wrong – the design research project draws its inspiration from the outer tissue layer of the cow’s intestine. This extremely thin, elastic and tear-resistant membrane, also called gold beater’s skin, was used in the past as a separating layer when beating gold leaf.
Product designers Robin Hoske and Felix Rasehorn, founders of WINT Design Lab, together with Mimotype Technologies, saw the potential in the material to create durable and recyclable high-performance textiles free of plastic.

Animal skins, due to their properties, have been used by humans throughout history to create textiles with water-repellent capabilities. During a one-year research fellowship, WINT therefore investigated the aesthetic and functional design features of the skin of the goldbeater and sequenced the RNA. The goal: to synthetically replicate the material properties, develop a biopolymer and use it to make high- performance textiles. In cooperation with Mimotype
Technologies, a biotech start-up from Berlin, and funded by the BIOTEXFUTURE project of the ITA Institute of Textile Technology, the researchers succeeded in cultivating the unique material in bioreactors. The result is bio-synthetically grown collagen substrate – vegan and biodegradable – from which WINT has reated a running jacket that meets both aesthetic and functional demands.
While the global demand for synthetic textiles continues to rise and their production consumes large amounts of petrochemicals, energy and finite raw materials, a new generation of water-repellent outdoor jackets is thus born.

Source: GOLD

Source: GOLD

Source: GOLD
“As designers we have to shift the reasoning of our practice from convenience to impact.”
———————————————————————–
THIS MIGHT BE ALSO INTERESTING FOR YOU:
Fabric Trends Spring.Summer 25 – Part II
27. February 2024
It's safe to say that a return to joy and lightness is in the air in the world of fashion!
The latest accessory developments for Spring.Summer 25 – Part I
22. February 2024
A big part of the collection consists of natural fibers with super light ribbons in 100% cotton, a linen braid-effect ribbon and hemp ribbons for a sustainable-oriented collection.
Fabric Trends Spring.Summer 25 – Part I
20. February 2024
It reflects the longing for positivity and offers new graphics, colours and weights. Summer is the perfect time to show character and put the shirt at the centre of the outfit. centre of the outfit.
Let's get circular - Sustainable innovations
Using existing resources and creating something new from them: What if you didn’t dispose of the leftovers of freshly squeezed juice – but could create a new material from it? Germany is at the forefront of apple juice consumption, producing up to 200,000 tonnes of pomace per year, solid residues from the pressing process. Instead of reusing them, as has been the case up to now, mainly in biogas plants, for pectin extraction or as animal feed, textile and surface designer Verena Brom has been inspired to develop new material systems for various industries.
The designer studied at the Weißensee Art Academy in Berlin. In the project “A Matter of Fruit“, she produces various biodegradable films from pomace residues that can be used instead of synthetic material. Visually and characteristically, it can be classified as a paper, plastic or leather alternative, depending on its thickness, and offers potential for different areas of application – from interior design to the clothing industry. The material is suitable for laser cutting and engraving, but due to its fusibility it can also be welded or pressed into shape. In addition to the films, Verena Brom has developed a printing paste made from apple pomace that further expands the material’s design possibilities and areas of application.
After the first cycle of use, the material can be returned to the natural loop: For example, it can be turned into a plant pot that biologically decomposes after being potted into the soil. This brings Verena Brohm closer to her goal of using renewable resources – such as the by-products of the food industry – and to use design as a tool to optimise material cycles.





“When developing the material, it was important to use as few additives as possible – and to push boundaries:
how can different properties be developed solely through different processing methods? Using different techniques can expand the
scope for design and influences the haptic and translucency of the material:
from smooth to abrasive, from transparent to opaque – a big variety of options are possible without loosing the mono-materiality.“
———————————————————————–
THIS MIGHT BE ALSO INTERESTING FOR YOU:
Fabric Trends Spring.Summer 25 – Part II
27. February 2024
It's safe to say that a return to joy and lightness is in the air in the world of fashion!
The latest accessory developments for Spring.Summer 25 – Part I
22. February 2024
A big part of the collection consists of natural fibers with super light ribbons in 100% cotton, a linen braid-effect ribbon and hemp ribbons for a sustainable-oriented collection.
Fabric Trends Spring.Summer 25 – Part I
20. February 2024
It reflects the longing for positivity and offers new graphics, colours and weights. Summer is the perfect time to show character and put the shirt at the centre of the outfit. centre of the outfit.
The New World of Colours - Sustainable innovations
THE NEW WORLD OF colours
MycoColors by Birke Weber and Friederike Hoberg
SUSTAINABLE INNOVATIONS
Dyes play a major role in our daily lives – in the clothes we wear, the cosmetics we use or the food we eat. Most of the dyes we use are of synthetic origin, which poses potential health risks – both in the manufacturing process and in the dyeing process or use. In addition, dyes and pigments in industrial wastewater are not infrequently released into the environment, where they remain and damage ecosystems.
MycoColors, a project by designer Birke Weber and biochemist Friederike Hoberg, addresses precisely this problem. The two are researching the potential of alternative dyes – specifically: from fungi. With MycoColors, they want to develop optimal growth conditions for colour-producing mycelium with the aim of creating a sustainable extraction of dyes and an innovative dyeing process and establishing fungal dyes in the textile and fashion industry. Because: fungi offer a lively, broad colour spectrum that runs through all the colours of the rainbow and is far from being exhausted


The advantages: The fungal mycelium from which the dyes are extracted grows within just a few days, cultivation takes place in inexpensive culture mediums and production is independent of weather and season. Furthermore, MycoColors works in a closed material cycle: resources such as water and nutrients can be recovered and reused, and by-products such as the biodegradable mycelium can either be returned to nature or upcycled – for example, by using it for paper production.
“The textile and fashion industry uses vast quantities of toxic and carcinogenic chemicals, including synthetic dyes, for its ever-changing
product range. But the end customers cannot trace everything that is hidden in a purchased T-shirt or carpet. A humane and environmentally
friendly alternative made from fungi aims to revise this uncertainty, especially with regard to the colors in a purchased product.”



———————————————————————–
THIS MIGHT BE ALSO INTERESTING FOR YOU
Fabric Trends Spring.Summer 25 – Part II
27. February 2024
It's safe to say that a return to joy and lightness is in the air in the world of fashion!
The latest accessory developments for Spring.Summer 25 – Part I
22. February 2024
A big part of the collection consists of natural fibers with super light ribbons in 100% cotton, a linen braid-effect ribbon and hemp ribbons for a sustainable-oriented collection.
Fabric Trends Spring.Summer 25 – Part I
20. February 2024
It reflects the longing for positivity and offers new graphics, colours and weights. Summer is the perfect time to show character and put the shirt at the centre of the outfit. centre of the outfit.
Collective braiding - Sustainable innovations
A world where everything is becoming faster, more connected and more digital, endless possibilities are emerging. But why always strive for the new instead of continuing the traditional?
Designer Camille Champion has taken note of this development and, during a stay in South Korea, set out to revive interest in traditional craftsmanship.


During her travels, she discovered the over 500-year-old technique of jiseung – a process dating back to the Joseon Dynasty that is used to make basketry from old books and paper waste. To do this, the paper is cut into thin strips and then corded. The cords can then be woven into containers such as baskets in various colours and patterns using different basketry techniques.
To save this cultural heritage from extinction, Camille Champion has launched the “Twist and Roll” project, bringing the reuse of newspaper waste to create new objects into a modern Western context: to pass on the craft, the designer has set up a series of workshops to give school children a connection to this tradition. She has designed a small weaving tutorial to teach children to make their own paper threads, weave them on a loom and then collectively build a tent-like structure for their classroom. Twist and Roll combines sustainability, creativity, craft skills and teamwork to show how the education system can benefit from crafts.

“In my opinion, giving the right tools to the new generations is very important.
Teaching them about materiality, history, or sustainability, will allow them to make the right choices for a better future.”
———————————————————————–
THIS MIGTH BE ALSO INTERESTING FOR YOU
Fabric Trends Spring.Summer 25 – Part II
27. February 2024
It's safe to say that a return to joy and lightness is in the air in the world of fashion!
The latest accessory developments for Spring.Summer 25 – Part I
22. February 2024
A big part of the collection consists of natural fibers with super light ribbons in 100% cotton, a linen braid-effect ribbon and hemp ribbons for a sustainable-oriented collection.
Fabric Trends Spring.Summer 25 – Part I
20. February 2024
It reflects the longing for positivity and offers new graphics, colours and weights. Summer is the perfect time to show character and put the shirt at the centre of the outfit. centre of the outfit.
Clothes that grow - Sustainable innovations


Nature as a 3D printer: material designer and underwater photographer Zena Holloway creates shapes and forms from wheat grass roots that grow in self-carved moulds made of beeswax. The supposed magic lasts for twelve days – the roots spread out horizontally or vertically and make their individual way through the wax templates. Depending on the shape of these, the roots either grow small in a confined space so that they become flat and compact, or if there is more space they can root deeper and three-dimensional shapes emerge. Immediately after harvesting, the roots are heavy and moist, after 24 hours they dry out and become light as a feather.
Each growth cycle produces a different result – all products are therefore individual pieces that can be further shaped by cutting, sewing, tearing or linking. For example, they can be used to create large, hanging structures, to shape vessels or to produce clothing and accessories. The wheatgrass roots also react particularly well to natural dyeing processes. In the name of sustainability: the water that accumulates and runs off during production can be reused and the leftover shoots, seeds or roots can be reused as animal feed. In addition, the dried root is a kind of botanical skeleton that binds carbon. Thus, the Rootful project demonstrates a micro-level approach to solving the complex problem of climate change.
“Growing artefacts from root is the simplest concept but captures the imagination of a wide audience.
I’m learning that root is a wonderful material to create fashion and art, serving to open up conversations around materiality and sustainability that inspire change.“
In the name of sustainability: the water that accumulates and runs off during production can be reused and the leftover shoots, seeds or roots can be reused as animal feed. In addition, the dried root is a kind of botanical skeleton that binds carbon.
Thus, the Rootful project demonstrates a micro-level approach to solving the complex problem of climate change.

———————————————————————–
THAT MIGHT BE ALSO INTERESTING FOR YOU
Fabric Trends Spring.Summer 25 – Part II
27. February 2024
It's safe to say that a return to joy and lightness is in the air in the world of fashion!
The latest accessory developments for Spring.Summer 25 – Part I
22. February 2024
A big part of the collection consists of natural fibers with super light ribbons in 100% cotton, a linen braid-effect ribbon and hemp ribbons for a sustainable-oriented collection.
Fabric Trends Spring.Summer 25 – Part I
20. February 2024
It reflects the longing for positivity and offers new graphics, colours and weights. Summer is the perfect time to show character and put the shirt at the centre of the outfit. centre of the outfit.
Hairy affair - Sustainable Innovation
Hair creates identity – we dye it, style it, create new looks and expressions, and associate ourselves with cultural or social groups. It loses meaning and becomes rubbish to be discarded. In her hair project, Savine School gives hair a second life.

“Haar Haar focuses on the short switch from appreciating hair to feeling disgusted by it, even when it is the same material. It seeks to give a second life
to the material we treasured when it was on our head.“

Every month, the textile designer and material researcher collects kilos of hair from various hair salons and extension studios and sorts them by colour and length. In the next step, she uses a machine to spin the hair together with wool into a uniform, flexible yarn. This yarn highlights the properties of both materials: the admixed wool offers the possibility to work with other tones beyond the hair colours, while the reflection of light on the hair provides a beautiful shimmer.
The designer uses the yarn to produce stylish accessories, such as crocheted hats – which at first glance have nothing to do with what ends up on the floor during a visit to the hairdresser. In this way, Savine Schoorl makes it clear that hair is a valuable resource and gives people the opportunity to discover the value of supposed waste in its second life cycle.

———————————————————————–
THIS MIGHT BE ALSO INTERESTING FOR YOU:
Fabric Trends Spring.Summer 25 – Part II
27. February 2024
It's safe to say that a return to joy and lightness is in the air in the world of fashion!
The latest accessory developments for Spring.Summer 25 – Part I
22. February 2024
A big part of the collection consists of natural fibers with super light ribbons in 100% cotton, a linen braid-effect ribbon and hemp ribbons for a sustainable-oriented collection.
Fabric Trends Spring.Summer 25 – Part I
20. February 2024
It reflects the longing for positivity and offers new graphics, colours and weights. Summer is the perfect time to show character and put the shirt at the centre of the outfit. centre of the outfit.
A Suit of Armour - Sustainable innovations

The name says it all: “Choub” means “wood” in Farsi – the material that designer Mehdi Mashayekhi draws on in his project Choub and uses innovative methods to create something new: Using digital fabrication, he has designed an abstract clothing collection for which he deconstructs the wood, giving the material new physical properties such as flexibility and stretchability.
The designer resorts to two methods: with topology optimisation, a computer-based process, he uses algorithmic models to determine the optimal shape of components in terms of load limits. The generative design method also creates new, powerful design options with the help of artificial intelligence. In this way, Mehdi Mashayekhi succeeds in solving complex requirements, distributing the weight of components and reducing manufacturing costs.

“Design is a glowing point in the cross-point between art and science, where reality meets vision.”

Innovative, unconventional, visionary: In the Choub project, 6mm thick plywood is used to create armour-like, portable constructions in which the wood loses its hardness and becomes flexible. Win-win: The designer optimises the use of materials in the design and at the same time provides a solution for upcycling waste. With the use of digital manufacturing, Mehdi Mashayekhi is helping to drive circularity and strengthen openness to materials and technical textiles.

———————————————————————–
THIS MIGHT BE ALSO INTERESTING FOR YOU
Fabric Trends Spring.Summer 25 – Part II
27. February 2024
It's safe to say that a return to joy and lightness is in the air in the world of fashion!
The latest accessory developments for Spring.Summer 25 – Part I
22. February 2024
A big part of the collection consists of natural fibers with super light ribbons in 100% cotton, a linen braid-effect ribbon and hemp ribbons for a sustainable-oriented collection.
Fabric Trends Spring.Summer 25 – Part I
20. February 2024
It reflects the longing for positivity and offers new graphics, colours and weights. Summer is the perfect time to show character and put the shirt at the centre of the outfit. centre of the outfit.